White Paper: A day in the life of a fiber optic technician
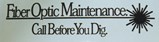
By Jennifer A. Briscoe, Sprint Corp.
Telecommunication is an integral part of our daily lives. Every time we make a phone call, send an e-mail, or get on the Internet, we are enlisting the help of telecommunications networks. The importance of those networks is increasing, as they are now mission-critical components of business. Protecting those networks has thus become the work of many a fiber optic technician — network specialists that safeguard telecommunications networks from outages that can disrupt and prevent vital communication.
Fiber optic technicians are responsible for patrolling miles of fiber optic cable. They are the skilled individuals that repair fiber cables severed by backhoes and other machinery--a full-time job, especially in good economic times when construction is high. In 1999, for example, Sprint experienced 61 fiber cuts. In addition to guarding the network and splicing fiber, technicians upgrade and maintain network equipment, supervise construction digs, integrate new fiber into the network and work to prevent fiber cuts from occurring in the first place.
I spent a day with one such technician in Charlottesville, VA—Jerry Vestal. Jerry became a full-time Sprint employee in 1988, after having worked as a microwave systems contractor for Sprint. He discovered his interest in electronics and fiber optics while serving in the US Marine Corps, earned a degree in management from Southern Illinois University, then began his career in technology. Our day began early in the morning at the Sprint point of presence (POP) site in Charlottesville, one of the three sites for which Jerry is officially responsible.
7:00 a.m., April 27, 2000
"My mornings revolve around CBYD (pronounced seebud)," said Jerry, the 37-year-old Sprint fiber optic technician. "Oh no, not another acronym," I thought to myself, not realizing how important that particular acronym is to the safety of telecommunications and data communications networks. "Call before you dig," Jerry explained, "is the phrase we use constantly to remind people that they need to call us 48 hours in advance of any activity that may involve digging." Construction crews rely upon fiber optic technicians to determine where fiber-optic lines are located so when digging, crews can avoid cutting through fiber optic cables.
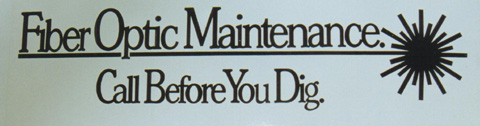
"One of the hardest things we faced when the fiber was first installed back in 1987," Jerry said, "was convincing construction contractors that these ‘skinny little cables' were not ‘just another couple of phone lines' and that it was imperative that we keep them intact. Our warning to ‘call before you dig' was so vigorous and persistent that the Sprint One Call Center adopted the acronym CBYD and it's been with us ever since," Jerry explained. Over time and as a result of the CBYD campaign, Jerry has seen Sprint's fiber optic cable go from ‘just a couple of phone lines' to ‘fiber optic cables?! I'm not digging anywhere near those unless I have to!'
Jerry is scheduled to work Monday through Friday and is typically on call three weekends per month. His day usually begins around 7:00 a.m. He arrived at the Sprint POP site extra early to greet me and begin his day. After a quick tour of the site, Jerry accessed a database via laptop housing "tickets" with information about upcoming construction work and digs taking place within his regional coverage areas.
"When construction is scheduled with Miss Utility of Virginia, Sprint's One Call Center, now also known as CBYD, is notified. CBYD organizes the tickets by area, then delivers them, in the form of this database, to regionally-assigned technicians, like me, so that we can evaluate whether or not the dig may jeopardize our cables," he explained. Once the tickets were downloaded — 63 total — Jerry reviewed each one, checking on the nature and location of the dig and its proximity to Sprint's fiber optic network.
"Some digs pose no threat to the cables, while others can be quite menacing," he warned. When a ticket describes a dig that can potentially harm Sprint's fiber network, Jerry makes plans to supervise the dig and enters information about next steps back into the database. That information then goes back to CBYD and then to Miss Utility, which delivers the next steps back to the call initiator. Sometimes Jerry wakes up early to download tickets from home in case a dig is taking place nearby. On this day, there were no menacing digs.
Jerry also maintains his sites' equipment, implementing upgrades and repair work, "The advances in equipment and technologies, like the synchronous optical network (SONET) and dense wave-division multiplexing (DWDM), have been amazing. The amount of traffic riding over the network has exploded, but less and less equipment is required to handle that traffic," said Jerry. For example, the Sprint network can send 1.5 million voice calls over a single fiber pair.
8:00 a.m.
After determining and recording notes regarding the course of action, or non-action, for each ticket, Jerry uploaded the notes into the database. Jerry's responses were then ready to be routed through the system, and ultimately relayed back to the ticket initiators so that they would be aware of any actions necessary to preserve the safety of nearby fiber.
9:00 a.m.
After the database upload, Jerry checked his e-mail. E-mail is Jerry's primary mode of communication with co-workers and e-mail messages often contain information about activities that need to take place at his POP sites. Jerry supervises three sites on his own, the Charlottesville and Lynchburg, VA, POP sites and the Buena, VA, regeneration site, and takes care of the activities involving the sites' operations, such as circuit provisioning, maintenance, and upgrades. When on call, Jerry is responsible for nine additional sites.
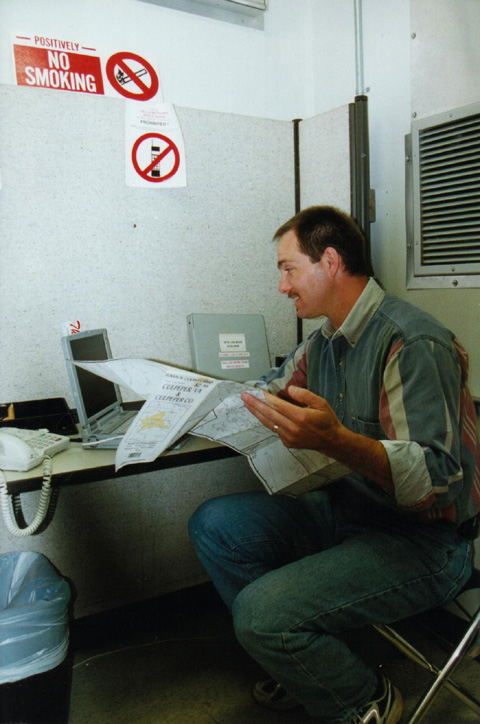
"I like this job because I'm given a lot of independence and responsibility. My supervisors know and trust that I will do my job as best I can and they give me the autonomy to make my own decisions. That gives me a real sense of responsibility and, as a result, commitment to my position," he said. In fact, when asked to list two of his most favorite things about being a fiber-optic technician, the first thing Jerry mentioned was the independence he has in his work and the responsibility that ensues.
The second thing Jerry likes best about his work is that his job description is very broad. He is involved in a wide variety of network operations and management. " I don't do the same thing every day. In fact, sometimes, on a moment's notice, I may have to travel half way across the state, or even outside of the state," he smiled. Jerry enjoys the spontaneity, "It's nice to have breaks from the every day routine," he said.
10:00 a.m.
After checking and returning e-mail, Jerry scheduled "jeopardy time" with the Sprint Network Control Center, located at Sprint's headquarters in Kansas City, KS. Technicians schedule jeopardy time when there is a risk that a system may be interrupted.
"Jeopardy work is commenced at night, when the amount of network traffic is at its lowest," he explained. Jerry will admit that he's not ecstatic about working at night, but he understands the risks and is more than willing to help make sure that the network is out of harm's way. While scheduling jeopardy time, Jerry also determined the MOP, or method of procedure, for the network operations. MOPs inform other project workers about the fiber-related activities that will be taking place, as well as the sequence of activities. In this particular case, the team will be integrating a new building's communication lines into already existing lines.
11:00 a.m.
A lot of Jerry's work involves phone communication with contractors, supervisors, construction crewmembers, and control center operators, all of which are involved in the coordination of a successful dig. He contacted a contractor with a regional bell operating company (RBOC) to obtain an update on the status of a railroad construction project. Then he contacted his supervisor to assist in determining who could oversee a dig taking place outside of his coverage area.
1:00 p.m.
Part of Jerry's role as a network operations specialist is making sure that the POP sites' equipment is functioning optimally. "Every network operating system in the US is monitored 24x7 by Sprint's Transport Control Center (TCC) in Kansas City. When a considerable degradation in fiber optic signaling occurs, the network's equipment goes into alarm mode. The TCC is notified of the alarm-generating signal degradation via telemetry, after which it alerts the technician responsible for the area in which the degradation has occurred so that we can conduct necessary repairs," Jerry explained. A few days prior to our meeting, Jerry had been notified of a signal degradation in his area and, after some trouble shooting, determined that an optical receiver had caused the alarm and needed repair. Upon returning to the POP site after lunch, Jerry received a fax with the information he needed to return the non-working optical receiver to its manufacturer.
So far, no fiber cuts. In fact, the last fiber cut in Virginia occurred in the city of Newport News in 1988. So, to give me a glimpse into what happens when there is a fiber cut, Jerry spliced an optical fiber. After stripping the tiny hairs of fiber from their thick black shell (called the outer sheath), their metal enclosure (called the armor) and then from their inner sheath, Jerry removed the fibers from their thin color-coded plastics (called buffer tubes and used for identification purposes) and placed two strands of fiber into his splicing machine. After aligning the two strands with each other, he activated the splicer and the two separate strands of fiber fused into one. "As you can see, permanently restoring fiber optic lines is a time-consuming activity. That's why Sprint has deployed SONET — a technology that, in the event of an outage, reroutes network traffic in milliseconds down a different path to its destination," Jerry explained. SONET is the main reason Sprint's customers continued to receive service in spite of 61 fiber cuts in 1999.
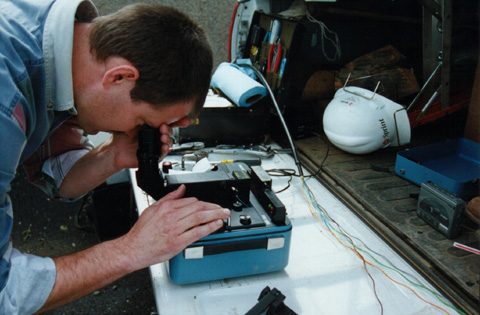
2:00 p.m.
Next, Jerry demonstrated how underground fiber optic cabling is located. "It's important that the exact location of the fiber be determined so that construction crews do not mistakenly cut through, or even near, the cables," he explained. First, Jerry activated a transmitter that sends signals through the cable. Then, as we walked outside, he turned on a receiver to detect the signal. The receiver's screen conveniently displayed directional arrows, directing us to the location of the fiber, making a distinct noise to let us know of its exact whereabouts.
"Right here," said Jerry as he handed me the receiver. He then took a can of bright orange spray paint and marked the location of the fiber. Bright orange is the color used to mark communication lines and construction crews are familiar with the color and its implications. "If an actual dig were taking place, we would be required to dig a hole in the ground (called pot-holing) to determine the exact location of the fiber."
3:00 p.m.
Today has been a mild day, no fiber cuts, no threatening digs. So Jerry taught me more about his day-to-day activities and gave a demonstration of an optical time domain reflectometer (OTDR), a device that can determine the distance to a problem on a fiber network, such as a break, making it a useful tool in optical network trouble-shooting. For example, after splicing a fiber, Jerry uses the OTDR to make sure that the splice has not caused a degradation, or loss, in the fiber's carrying ability. The OTDR can also help detect problems with network equipment, as it provides a visual analysis of the health of the fiber.
4:00 p.m.
Jerry's day typically ends around 4:005:00 p.m. In closing, he offered insight into the qualities and characteristics a person might need to complement a job such as his. They included: self-starting/motivated, independent, confident, focused but flexible, and the ability to interface with many personalities.
"Another thing I like about my work is that I have the opportunity to interact with many different people: crew workers, contractors, other Sprint technicians and employees. In other words, I could be shaking hands with someone in a business suit in the morning then digging a hole with someone in torn jeans and a worn out T-shirt in the afternoon," he said smiling.
Of course we would not neglect to mention the job's downsides. Jerry said that two things he would cite as his job's downsides would be:
- His hours are not always the same—he sometimes has to work at night and on the weekends (jeopardy time)
- Jerry is almost always "on call." Because most scheduled maintenance occurs during weekends, he is typically on call three weekends per month. When on call, he is responsible for a total of 12 sites, many of which are geographically dispersed. He never truly leaves his job when he goes home since, on a moment's notice, he may need to tend to a network or POP site emergency
Other Facts and Findings:
- He frequently attends classes to keep informed of new technologies and equipment
- His Sprint truck is filled with equipment and other gear that enable him to perform field work quickly and efficiently; e.g., rain gear, fiber cable locators, shovel, an extra set of clothing, food and, of course, fiber
"Finally, it's important to tell people about our sense of ownership," said Jerry. "The Sprint network is our network and we take it personally when someone or something threatens it. When it comes to maintaining the integrity of Sprint's network, the buck stops here. We're the last defense to maintaining great customer service."